DIEP AT YOUR SIDE.
We really get deep into the subject matter.
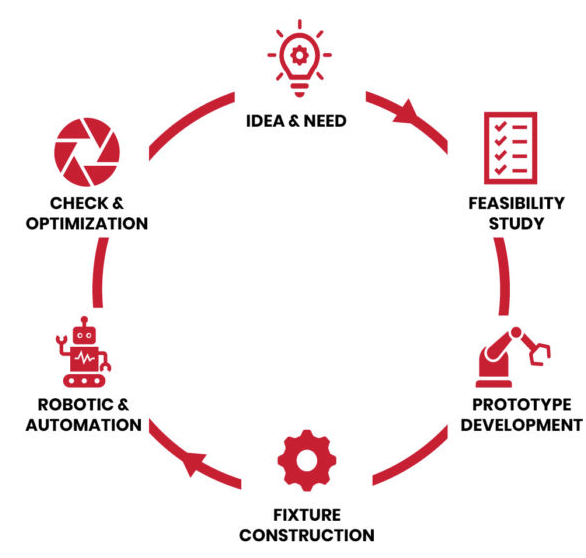
DIEP-Technology's pragmatic end-to-end approach.
The desire or urge for process changes, the constant optimization of production and business processes, occurs in every company. The implementation is mostly lacking due to insufficient personnel or technical capacities or the well-known tunnel vision of the loyal employees. DIEP-Technology supports this very early process of analysis and brainstorming through the evaluation of solution approaches to transformation.
more
At the heart of product development are:
- feasibility studies
- prototype development> design and industrialization
- jig construction
- Robot and camera applications> Bin Picking (bin picking), Pick & Place, MRK (Machine-Robot-Collaboration)
- Automations with and without robots, camera and sensor guided robot applications
- Quality monitoring systems (pre and post monitoring) with camera checks, GLD checks, sensor checks and calibrations
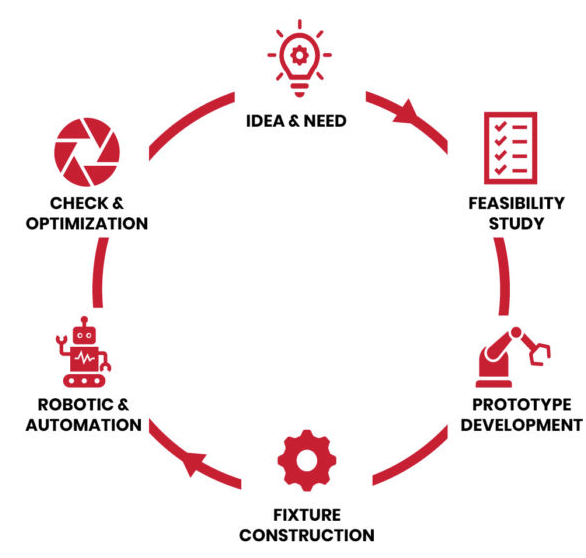
DIEP-Technology ‘s pragmatic end-to-end approach.
The desire or urge for process changes, the constant optimization of production and business processes, occurs in every company. The implementation is mostly lacking due to insufficient personnel or technical capacities or the well-known tunnel vision of the loyal employees. DIEP-Technology supports this very early process of analysis and brainstorming through the evaluation of solution approaches to transformation.
At the heart of product development are:
- feasibility studies
- prototype development> design and industrialization
- jig construction
- Robot and camera applications> Bin Picking (bin picking), Pick & Place, MRK (Machine-Robot-Collaboration)
- Automations with and without robots, camera and sensor guided robot applications
- Quality monitoring systems (pre and post monitoring) with camera checks, GLD checks, sensor checks and calibrations
Full-service provider in the implementation.
DIEP-Technology offers its customers the complete package for the implementation of the previously developed solution approaches. Following the workshop and the resulting solution conception, the project is planned and discussed with the company, suppliers and, if necessary, external suppliers under our leadership up to production capability.
PLANNING
- workshops
- Profitability calculation
- layout
- Project
- Solutions
TRANSFORMATION
- Creation of plant layout
- Kick Off & Release
- Detailed drawings
- Creation of E-Plan & P-Plan
- Wiring & mechanical assembly
- programming
- Pre-acceptance
- Disassembly & shipment to customer
- Commissioning & Training
- Final acceptance
DOCUMENTATION
- CE & Declaration of Conformity
- E plan
- Pneumatic plane
- training documents
- Instruction manual
Professional training on site in the company.
DIEP-Technology uses the mobile training cell for on-site training at the company. The training robot is a fully functional industrial robot that employees use to test feasibility and run experiments on operational topics and projects. Using this pragmatic robot training, we set up an internal team of experts at low cost.
Our trainers all have the relevant KUKA certificates. We can document well over 550 hours of training experience and over 270 positively trained participants from international corporations, medium-sized and family businesses.
Your advantages of our in-house robot training:
- Training in the company (cost advantage, as there are no travel and hotel costs for the participants)
- Smaller groups with min. 2 to max. 4 people, so that our trainers can respond to questions individually.
- Discuss user cases on site in order to have immediate operational reference
- Training documents developed together with KUKA and based on them as a reference work.
- Shorter duration of the training courses (employee absences are kept to a minimum).
Our workshops: Hands-on practice
DIEP-Technology would like to promote automation with robots in its constant activity. It is important to generate and convey enthusiasm and understanding. We like to take a pragmatic approach and look for topics from the immediate environment of the employees. Cycle time and processes are critically questioned and analyzed. The goals are to increase or improve productivity and ultimately profitability.
DIEP-Technology uses proven tools, such as the effective innovation management tool GEMBA. Understandable strategies for process development are developed together, structured into operative goals and concrete measures for implementation are worked out. DIEP-Technology tries to convey the holistic approach to the change process and to internalize it with the participants.